Custom Equipment Integration: A Competitive Edge
Off-the-shelf solutions often fall short when it comes to complex electrical systems. That’s where custom equipment integration steps in not just as a solution, but as a strategic advantage. For electrical contractors, the ability to integrate custom equipment into facility power systems, automation networks, and control panels is no longer optional; it’s an expectation for high-performance, future-ready operations.
Recore has built a reputation as one of the Carolinas’ top electrical contractors by meeting these complex needs head-on. Through engineering support, precision installation, and ongoing service, Recore’s approach to custom equipment integration delivers long-term value for clients in manufacturing, energy, data, and infrastructure sectors.
What Is Custom Equipment Integration?
Custom equipment integration refers to the process of designing and installing electrical systems that work seamlessly with specialized machinery or unique operational requirements. Rather than adapting the facility to the equipment, integration adapts the electrical system to meet the precise needs of the equipment.
This can include:
- Control panel fabrication for proprietary machinery
- Integrating variable frequency drives (VFDs) with legacy motors
- Programming PLCs for custom process control
- Supporting data acquisition and SCADA systems
- Matching power supply systems to equipment startup sequences
- Installing motor control centers (MCCs) built to custom load profiles
For facilities that run mission-critical processes or house high-value assets, such precision is essential.
Why Electrical Contractors Must Offer Integration Services
The demand for specialized equipment in industrial and commercial sectors is rising. According to the U.S. Department of Energy, advanced manufacturing facilities increasingly rely on interconnected systems and digital controls. These systems require more than just installation, they demand collaboration between mechanical, automation, and electrical teams.
Electrical contractors who can provide integrated solutions are in a better position to win projects where performance and uptime are critical. This can include:
- Food and beverage plants requiring CIP-compliant electrical layouts
- Manufacturing lines utilizing robotics and real-time analytics
In these settings, a standard install won’t suffice. Contractors must anticipate how each piece of equipment will perform within the facility’s broader ecosystem.
Benefits of Custom Equipment Integration
1. Improved System Performance
By designing electrical systems specifically for the equipment they support, contractors reduce inefficiencies and lower the risk of voltage drops, signal loss, or communication lag. Everything, from conduit layout to panel board sizes, is tailored to performance.
2. Reduced Downtime
Tailored systems offer fewer failure points and are easier to diagnose. When equipment, controls, and power systems are integrated from the start, service technicians spend less time troubleshooting mismatches or retrofitting solutions later.
3. Regulatory Compliance
Custom integration makes it easier to comply with industry-specific standards. For instance, the
Occupational Safety and Health Administration (OSHA) outlines requirements for machine safety, guarding, and control reliability. Integrated systems can be built with lockout/tagout functionality and e-stop zones from the beginning.
4. Scalability and Upgrades
Properly integrated systems are easier to scale. Adding a new production line or upgrading an existing component doesn’t mean redesigning the entire electrical infrastructure means building on a stable, organized, and documented system.
5. Long-Term Cost Savings
While custom integration may have higher upfront engineering costs, it prevents more expensive retrofits and downtime down the line. A properly designed system can operate efficiently for decades with routine maintenance.
What Custom Integration Looks Like on the Jobsite
Recore’s team works closely with clients, vendors, and engineers during the pre-construction and commissioning phases to identify the specific electrical requirements of each piece of equipment. This includes:
- Gathering technical specifications from OEMs
- Verifying voltage, phase, and current requirements
- Reviewing I/O maps and communication protocols
- Designing layouts that support both operator access and maintenance
- Fabricating UL-listed panels that match equipment inputs
- Programming VFDs and PLCs for load sequencing or motion control
- Running pre-commissioning checks before energizing
The process also involves careful documentation, labeling, and training to support long-term use and maintenance by client personnel.
Partnering for Success
Contractors who succeed in custom integration are those who build relationships with their clients and their suppliers. Recore’s network of OEMs, panel builders, and engineers makes it possible to deliver custom electrical systems that are as durable as they are innovative.
This relationship-based approach also helps clients navigate upgrades, replacements, or process changes in the future. Since the system was built to spec from the beginning, modifications can be executed with minimal downtime or risk.
Key Considerations for Facility Managers
If you’re managing an industrial or commercial facility, here are a few signs it may be time to seek a contractor who specializes in custom equipment integration:
- Your current electrical systems have been retrofitted repeatedly and now lack clarity or documentation
- You’re installing equipment from overseas that requires voltage conversion, frequency adaptation, or control system changes
- You’re launching a new product line that requires new motion, heating, or automation equipment
- Your team frequently experiences downtime due to compatibility issues between your systems and equipment
Working with a contractor who specializes in integration can help minimize startup delays, reduce long-term operating costs, and provide peace of mind that your systems are built with growth in mind.
Conclusion
As equipment evolves, so must the systems that power and control it. Custom equipment integration is no longer just a service, it’s a critical component of how leading electrical contractors deliver value.
Recore’s ability to support clients with tailored electrical systems, backed by technical expertise and a safety-first culture, is part of what makes the company stand out. From pre-construction planning to energized operations, Recore provides full-spectrum integration services that meet today’s complex demands.
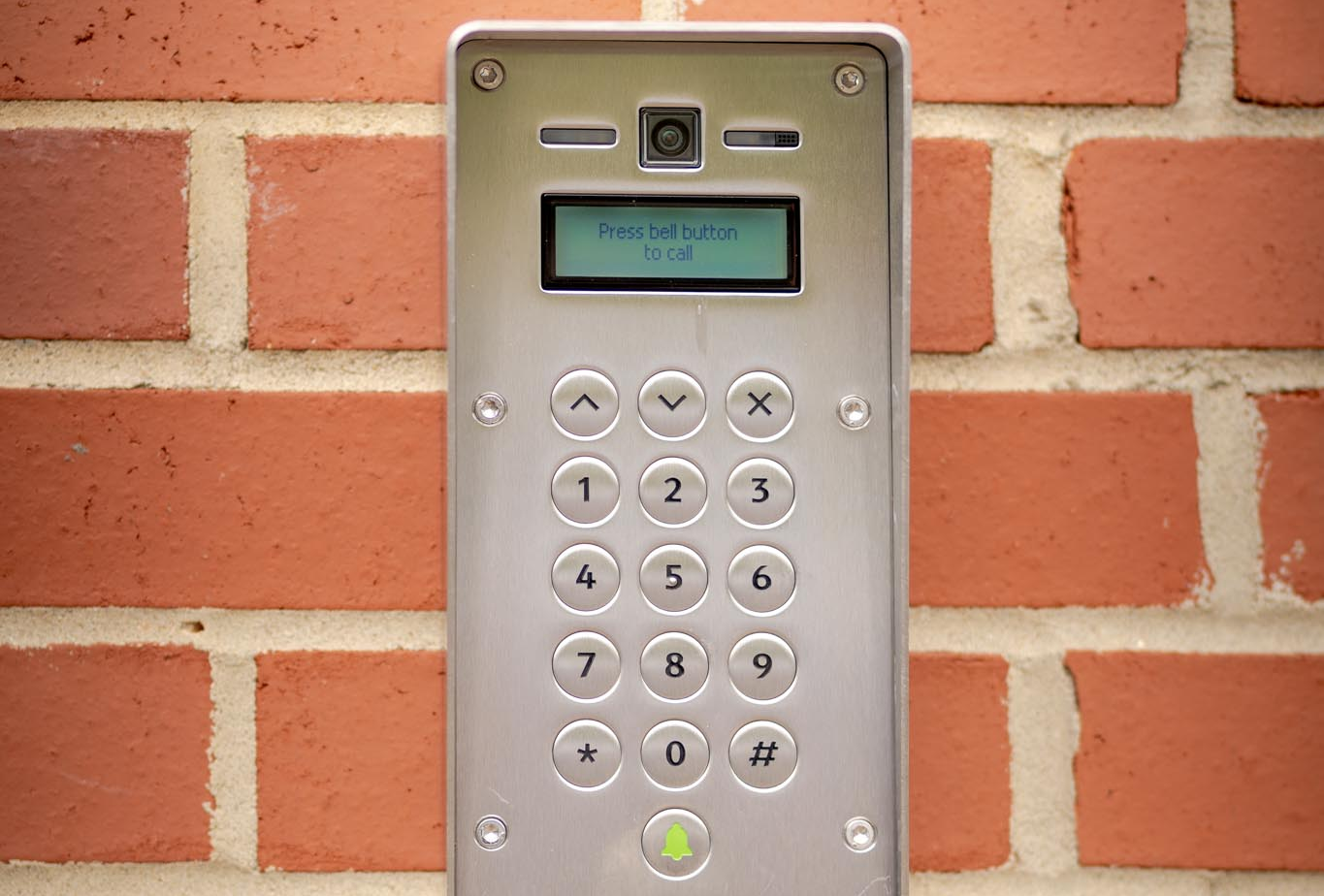